Inventory Management Tips to Keep Your Inventory Under Control
- borislyman371i
- Jun 10, 2022
- 2 min read
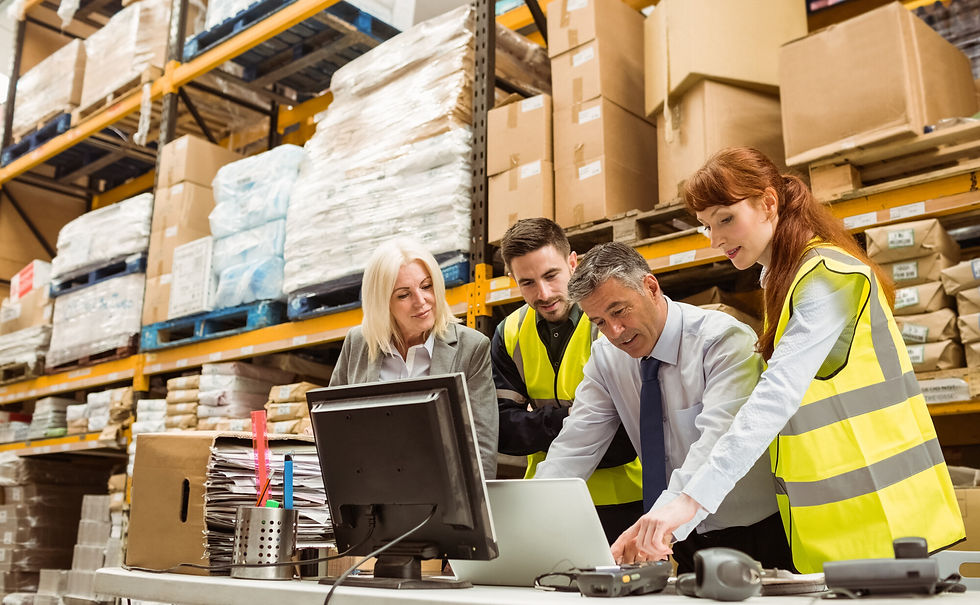
Good inventory management can save time, money, and human energy. Not only that, it can also decrease your stress levels. Aim for 100% customer satisfaction. This will help keep your business focused on its ultimate goal - customer satisfaction. After all, reviews and word of mouth are part of a company's reputation. By establishing a customer satisfaction goal, inventory management becomes less of a hassle. If you want to avoid costly mistakes, try these tips to keep your inventory under control.
Inventory management can be challenging, but using predictive analytics and other techniques can help counter these issues. One problem is a skills shortage that affects many industries. As a result, training employees may be necessary. This can be a challenge if employees are not experienced in inventory management. Luckily, there are many resources available that can help. In addition to a good software program, you can get training to learn specific practices that will help you improve your inventory management.
The process of inventory management consists of storing, handling, and disposing of goods. In other words, inventory is any material or goods that a company has with the intention of selling them. It can be raw materials, bulk products, and even intangible goods. In any case, every venture will need to manage inventory. The most important aspect of inventory management is that it allows the business owner to see exactly where their products are at any given time. Learn more about small business inventory management or see how to make work in progress inventory.
Stock levels vary between businesses. In the case of a handcrafted dining chair, a piece of wood needs six different sizes, as does the cushion. Sam purchases 10 planks of each size and ten cushions for each chair. He works hard turning these materials into chairs. Over time, the stock levels fluctuate. As a result, Sam must keep track of the materials and their quantities in order to sell them. A well-run business can make smart decisions by evaluating their inventory costs.
The oldest method of inventory tracking is manual counting. It requires shutting down operations and establishing teams to count the inventory. Moreover, manual counting is time-consuming and inefficient. Once inventory levels increase, it becomes difficult to keep track of the inventory. However, if you can afford the time, manual inventory counting is a great option for a small business. However, it is crucial to know the exact amount of inventory and how much is being used for what purpose.
The cost of goods sold (COGS) is another factor that must be considered when determining your inventory management strategy. This cost includes all the costs associated with the production of goods and the direct costs of selling them. Another method is economic order quantity (EOQ). This method is used for optimum order quantities in order to minimize total ordering costs. It is sometimes called optimum lot size. If you are unsure of how many units you need to order, you can use the minimum order quantity (MOQ). Continue reading more on this here: https://www.huffpost.com/entry/managing-inventory-is-key_b_10730018.
Comments